Melodi
Disaster Cat
I used to be on the Foxfire mailing list in the 1980s. She sent out samples of the colored cottons while describing the work that went into reviving colored cottons which had been lost since the fall of the Inca Empire. When the textiles were anyalized it was discovered many were not died, but that the cotton colors were natural - blues, greens, yellows etc. I thought this article was interesting and not too one-sided for the new (possibly GMO "Gene Altered" fabrics) - Melodi
modernfarmer.com
Are Next-Gen Synthetic Fibers the Future of Sustainable Textiles?
MAR 01, 2024
Sheila Pell
As research and production of next-gen synthetic fibers take off in search of alternatives to polyester, some natural fiber producers worry they’ll be left in the hamper.
A collection of materials from Spiber Inc., manufactured through fermentation of plant-based ingredients.
Photography courtesy of Spiber Inc.
Polyester was once thought to be a wonder fiber. Both durable and efficient, with no need for farmland or vast amounts of water, it threatened to leave natural fibers like cotton in the dust.
It turns out the miracle thread made from oil isn’t so recyclable. But it does break down, bit by bit: in the wash, on land, everywhere. Textiles are a major source of microplastics in the ocean, where they weave their way into the food chain, causing untold harms to marine life. Entire ecosystems are being altered by our clothes.
Studies tell us we eat and drink its flecks, too, with unknown health impacts, and that the volume of plastic particles in the ocean is doubling about every six years.
Our daily clothing choices are part of it all, but with polyester, rayon and acrylic so ubiquitous plastic even rains from the sky, choices are limited. Polyester, made from the same plastic as most water bottles, is woven into about half of the world’s clothing. Cheap and easy to make, it’s still the fastest-growing group of fibers used to manufacture garments.
What’s the solution? Some see the answer to more sustainable fabrics in new materials that can readily decompose or be recycled; others say natural fibers and local supply chains are the way to go. But each approach depends on infrastructure that has yet to be fully realized. If the end game is simply more mass production and consumption, with the thought that all of this material will quickly degrade or find its way to recycling, our oceans and landfills of trash will only grow.
The high cost of fast fashion
Fast fashion uses both synthetic and natural fibers, and the environmental trade-offs between the two are endless, from land and water use to chemical inputs. But when it comes to planet-heating emissions, fossil fuel-based synthetics—the main materials in use—are clear losers. Fashion contributes around 10 percent of global greenhouse gas emissions, second only to big oil. And most of the carbon footprint of a garment is around producing its fibers.
Another big factor is end of life. There is nowhere near enough fiber recycling infrastructure in the US, where 85 percent of used clothes and other textiles get sent to the landfill. In California, most clothing is disposed of through curbside solid waste collection—a straight route to the dump. At every level are gaps that prevent “textile circularity” especially when it comes to sorting out salvageable garments and sourcing recycling. And while natural fibers can biodegrade, it’s rarely that simple. Companies often blend natural with plastic fibers, adding dyes and finishes, and blends are particularly hard to recycle because the components require different processes.
In the US, 85 percent of used clothes and other textiles are sent to the landfill. (Photo: Shutterstock)
For companies, it isn’t profitable to develop large-scale reuse, repair and recycling with the high costs of transportation, labor and processing, along with decreasing quality of new products.
According to standards body Textile Exchange, only about 14 percent of polyester is made from recycled fibers. Companies are working on technology to make it easier—yet thousands of dangerous chemicals are used to make plastic goods and researchers are sounding the alarm about recycling them.
In addition, most natural fibers are grown conventionally, which often means heavy use of pesticides, synthetic fertilizers and genetically modified or treated seeds. Cotton, the most used natural fiber, occupies 2.4 percent of the world’s farmland but uses 4.7 percent of the world’s pesticides and 10 percent of its insecticides.
Enter next-gen synthetics. A slew of startups is out to replace both polyester and natural fibers with alternatives they say are better for the planet.
Emerging protein designers
One emerging method used to create new fibers is with gene editing. It happens in a wink compared to the millions of years it took nature and selective breeding by humans to perfect, say, sheeps’ wool.
After modifying genes that give a desired quality to a natural fiber, scientists insert this DNA into yeast or bacteria cells. Next, fermentation turns the microbes into factories, churning out proteins that will be spun into fibers and given names such as Microsilk and Werewool.
As the companies see it, the process is more efficient than growing fibers naturally; traditional silk, for example, is biodegradable and long-lasting, but cultivation can use large amounts of water and pesticides. One of the most promising polyester and silk replacements is Tandem Repeat’s squid protein-based Squitex, which draws on AI to design a fiber with stretch, strength and thermal responsiveness, and it works with most current manufacturing equipment. The Philadelphia company, which plans to sell both fibers and garments, will release a limited collection this year.
Another is Spiber’s Brewed Protein, which can replace oil-based, silk and other animal fibers. The polymer can yield various end products depending on the twisting of yarns. By changing the protein content and yarn diameter, the company can tweak texture, weight and handfeel.
Spiber Inc’s Brewed Protein filament yarns have a silk-like sheen and texture. (Photo courtesy of Spiber Inc.)
That’s the easy part, experts say. The difficulty, and the stage most of these startups are now, is in scaling manufacturing. The manufacture of next-gen fibers requires giant fermentation vats and skilled workers. When it comes to spinning, according to Bloom Labs, costs can be two to three times higher than with oil-based yarns because the melt-spun machines used by the apparel industry don’t work with these fledgling fibers.
But as the planet burns and plastic fibers boom, it’s getting harder for brands to ignore the need for sustainable fabrics.
Nicole Rawling, CEO and co-founder of the think tank Material Innovation Initiative (MII), says they define “next-gen” as more than the gene-edited proteins. Those fibers can be plant-derived, mycelium, cultivated animal cells, microbe-derived, recycled materials and blends. “Next-gen materials must be animal-free, high-performance and have a smaller environmental footprint than their traditional counterparts,” she says. MII focuses on the goals of production, not the technologies used.
“We recommend focusing on the real problem: petrochemicals, not plastics,” says Rawling, noting that some plastics are bio-based and have less of an environmental impact. The claim is controversial, however, in terms of biodegradability and because plant-based plastics require crops such as corn and farmland that could have been used to grow food.
Spiber’s Brewed Protein materials are produced through a fermentation process that utilizes sugars and microbes. (Photo courtesy of Spiber Inc.)
Proteins aside, Circ, a recycling innovator, has developed a hydrothermal process that can separate polyester-cotton blends—the largest blend category globally—and recover both portions to make into like-new fibers for textiles.
“Not long ago, it was nearly impossible to separate and re-use fibers from cotton/poly blends, thus millions of tons of discarded clothing and textiles were destined for landfill or incineration,” says Rawling.
One challenge is designing biodegradability into goods that won’t easily fall apart in use. A recent study from UC San Diego’s Scripps Institution of Oceanography tracked the ability of natural, synthetic and blended fabrics to decompose in the ocean. It found that natural and wood-based cellulose fabrics (Lyocell, Modal and Viscose) degraded within a month, while fabrics made of what was thought to be a biodegradable plastic (PLA) and the oil-based fibers in textile blends showed no decay after more than a year in the ocean.
Kintra Fibers has developed a bio-based polyester (56 percent corn-derived) it says greatly reduces greenhouse gas emissions compared to conventional polyester and can be produced with the same equipment. According to its website, the material decays in controlled composting conditions.
Fiber growers
Last October, Sally Fox was thousands of miles from home, where the greens and golds of her cotton fields shimmered in the Central Valley sun. She was at a cotton-spinning mill in Japan to sell her fibers, because there are no such mills left in California, she said in an email. “I have one customer in the world.”
Fox has been selectively breeding cotton to produce her exquisitely colored yarns for 38 years, and she says the industry was once profitable enough that she could afford to lease her own gins, the machines that quickly separate cotton fibers from seeds.
That’s no longer the case. “The textile industry collapsed when the big brands went offshore and dumped the spinners and weavers in the US, Europe and Japan. And I lost all the mills I was selling to except this one,” she said.
Fiber farmers, already up against cheap polyester and the economy of fast fashion, now face another threat: the rise of mass-produced alternative synthetics in development.
Naturally colored cotton, bred by Sally Fox, growing at her Viriditas farm in California’s Capay Valley. (Photo courtesy of Sally Fox)
Rebecca Burgess, founder of Fibershed, a nonprofit that supports regenerative farming, points out that there is already a bounty of natural fiber available for textiles.
Two-thirds of the wool in California doesn’t even have a home and 900,000 pounds per year is textile grade, says Burgess. “We’re not even getting all the natural fibers that are part of food rotations.”
The US is the third-largest global cotton producer. In 2018, more than 14 million of the 18 million bales it produced were exported. More than 200,000 acres of cotton is grown in the San Joaquin Valley—”enough to create at least seven pairs of jeans each year for every person in the state,” says Burgess.
If a strong local fiber economy existed, growers could find markets for all their fiber, she says. Instead, they face “huge deficits” in aggregation, distribution and manufacturing. If you start a spinning mill, for example, you also need a good wool scour line for a washing station and places to send wastewater.
Absent is large-scale felting, wool scouring, color-grown cotton gins, large-scale fine gauge spinning, industrial felt natural dye pigment production and more.
Burgess sees the main problem with cheap fashion—one she thinks next-gen won’t solve—as massive overconsumption. At one end are people unboxing their huge hauls, “stoking people on TikTok to purchase just like them.” At the other is the Atacama Desert in Chile or Accra in Ghana, “where they receive something like 40 million garments per month,” most of which end up in open-air dumps.
Soil-to-soil fiber economies
Fibershed advocates for bringing home the once-thriving textile supply chain, which now exists as a geographically long series of links among growers and processors of fibers, weavers, knitters, dyers and finishers, product manufacturers and distributors. It envisions local systems where natural fibers are sustainably grown, processed, sewn into garments and ultimately composted.
In Fibershed’s 168-producer network are regenerative farms and textile projects such as Chico Flax in the Sacramento Valley, which is working on bringing back the region’s flax textile industry. There are growers of dye plants, hemp, cotton and wool.
Wool production is often criticized for wreaking havoc on land, from overgrazing to scouring chemicals. The Center for Biological Diversity has called on brands to phase out or cut wool use in half by 2025. But Fibershed sees wool as a carbon sink. More than 55 wool producers have joined its Climate Beneficial™ Verification label program that supports farmers who are building healthy soil.
Wool is a renewable, biodegradable resource, but critics say the current scale of wool farming is environmentally unsustainable. (Photo: Shutterstock)
It’s not about small versus large-scale farming, says Burgess; small growers don’t always have enough land to use the rotational grazing that fosters plant biodiversity. “Some of the most regenerative, or grassland regenerating, grazing I’ve seen is on larger operations.”
To create vegetation shifts and poly cultures, ranchers try to mimic a wildland biome through multi-species grazing, “moving animals quickly through these systems, then having them return after land has had time to regenerate.”
Even cotton can be grown and processed within a scalable, restorative system, proponents say. Central Valley growers and researchers are incorporating carbon farming to help soil store carbon and water; abilities lost to decades of conventional practices. Less than one percent of cotton grown in the US is organic.
Cotton growing at Viriditas Farm, where rotational crops like heirloom Sonora wheat bolster root material and straw to build soil organic matter with each crop year. (Photo courtesy of Sally Fox)
Cleaning up cotton is something Sally Fox knows all about. “I was among those who started the whole organic cotton industry.” She grows her colorful “foxfibre” cotton using biodynamic practices, but for certification, she sticks with organic—it’s less challenging, but organic is the original regenerative certification, she says.
“It is absolutely the gold standard for sequestering carbon into soils—the goal of all regenerative farming practices.”
Unbox ‘like new’
Fox views sustainability in clothing as revolving around its longevity. Cotton spun correctly should last 20 to 60 years (except jeans). Linen spun correctly should last 100 to 1,000 years. Wool spun properly should last 80 to 300 years. “I am not kidding,” she emphasizes.
Her next criteria is ethical production, “with the work force between the raw material and final product not being enslaved or coerced or any of the rest of the shenanigans used to beat down the cost brands pay for products.” She prefers garments made in the US, Japan or the EU, because they have workplace standards. Elsewhere, she seeks GOTS and Oeko-Tex certifications. “GOTS actually inspects every facility.”
Last but not least, she mends holes, fixes seams. She even darns socks. It’s not exactly fast fashion, but just landing on a definition of sustainable “can make one’s head spin,” she says. And the first response is to give up, and basically give in to polyester—the wonder fabric that, today, isn’t so wrinkle-free after all.
With legislation that requires end-of-life solutions for products, consumers rethinking their choices and investment in both next-gen synthetics and local natural fiber economies, both visions can be part of a better clothing future. Here’s how you can help:
Buy less, and love what you do buy. Instead of buying loads of cheap clothing, instead think about investing in a few high-quality items that you love and know will last you a long time. Whether made of synthetic fibers or natural fibers such as wool, silk and linen, keep in mind the lifecycle of your clothing: what will happen to it when you’re finished with it?
Buy and sell used clothing. Gently worn or returned purchases are increasingly being offered on sites such as ThredUp, Poshmark, Relay Goods and Patagonia’s Worn Wear. (For example, Relay, which calls itself a zero waste marketplace, sells shoes and sports gear, buying their surplus inventory and returns from retailers and offering the most sought-after shoes at attractive markdowns).
Learn to mend and repair. Sewing, darning and other forms of mending used to be common, and for good reason: they help you get the most out of your clothing, and they can be fun and creative, too. Inspiration is everywhere, if you know where to look—social media can be a good place to start, and books such as Visible Mending by Arounna Khounnoraj provide step-by-step instructions for how newbies can get started.
Support legislation designed to cut down on textile waste. Legislation introduced in California and New York would eventually require textile producers to provide end-of-life solutions for products. If you want to support those bills or ask for a similar one to be introduced in your state, contact your local legislators and let your voice be heard.
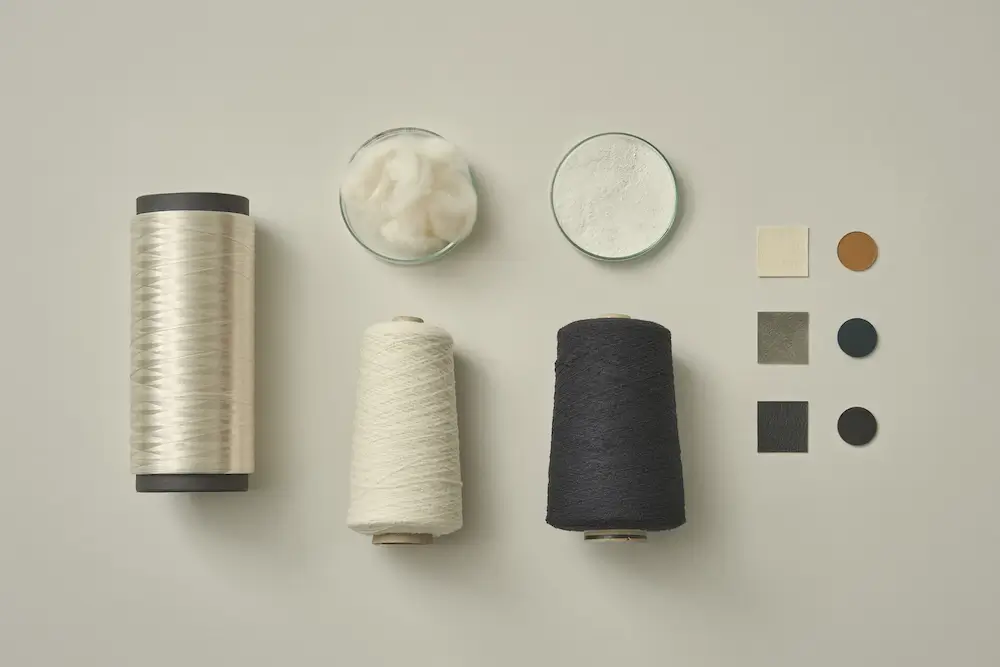
Are Next-Gen Synthetic Fibers the Future of Sustainable Textiles? - Modern Farmer
Polyester was once thought to be a wonder fiber. Both durable and efficient, with no need for farmland or vast amounts of water, it threatened to leave

MAR 01, 2024
Sheila Pell
As research and production of next-gen synthetic fibers take off in search of alternatives to polyester, some natural fiber producers worry they’ll be left in the hamper.
A collection of materials from Spiber Inc., manufactured through fermentation of plant-based ingredients.
Photography courtesy of Spiber Inc.
Polyester was once thought to be a wonder fiber. Both durable and efficient, with no need for farmland or vast amounts of water, it threatened to leave natural fibers like cotton in the dust.
It turns out the miracle thread made from oil isn’t so recyclable. But it does break down, bit by bit: in the wash, on land, everywhere. Textiles are a major source of microplastics in the ocean, where they weave their way into the food chain, causing untold harms to marine life. Entire ecosystems are being altered by our clothes.
Studies tell us we eat and drink its flecks, too, with unknown health impacts, and that the volume of plastic particles in the ocean is doubling about every six years.
Our daily clothing choices are part of it all, but with polyester, rayon and acrylic so ubiquitous plastic even rains from the sky, choices are limited. Polyester, made from the same plastic as most water bottles, is woven into about half of the world’s clothing. Cheap and easy to make, it’s still the fastest-growing group of fibers used to manufacture garments.
What’s the solution? Some see the answer to more sustainable fabrics in new materials that can readily decompose or be recycled; others say natural fibers and local supply chains are the way to go. But each approach depends on infrastructure that has yet to be fully realized. If the end game is simply more mass production and consumption, with the thought that all of this material will quickly degrade or find its way to recycling, our oceans and landfills of trash will only grow.
The high cost of fast fashion
Fast fashion uses both synthetic and natural fibers, and the environmental trade-offs between the two are endless, from land and water use to chemical inputs. But when it comes to planet-heating emissions, fossil fuel-based synthetics—the main materials in use—are clear losers. Fashion contributes around 10 percent of global greenhouse gas emissions, second only to big oil. And most of the carbon footprint of a garment is around producing its fibers.
Another big factor is end of life. There is nowhere near enough fiber recycling infrastructure in the US, where 85 percent of used clothes and other textiles get sent to the landfill. In California, most clothing is disposed of through curbside solid waste collection—a straight route to the dump. At every level are gaps that prevent “textile circularity” especially when it comes to sorting out salvageable garments and sourcing recycling. And while natural fibers can biodegrade, it’s rarely that simple. Companies often blend natural with plastic fibers, adding dyes and finishes, and blends are particularly hard to recycle because the components require different processes.
In the US, 85 percent of used clothes and other textiles are sent to the landfill. (Photo: Shutterstock)
For companies, it isn’t profitable to develop large-scale reuse, repair and recycling with the high costs of transportation, labor and processing, along with decreasing quality of new products.
According to standards body Textile Exchange, only about 14 percent of polyester is made from recycled fibers. Companies are working on technology to make it easier—yet thousands of dangerous chemicals are used to make plastic goods and researchers are sounding the alarm about recycling them.
In addition, most natural fibers are grown conventionally, which often means heavy use of pesticides, synthetic fertilizers and genetically modified or treated seeds. Cotton, the most used natural fiber, occupies 2.4 percent of the world’s farmland but uses 4.7 percent of the world’s pesticides and 10 percent of its insecticides.
Enter next-gen synthetics. A slew of startups is out to replace both polyester and natural fibers with alternatives they say are better for the planet.
Emerging protein designers
One emerging method used to create new fibers is with gene editing. It happens in a wink compared to the millions of years it took nature and selective breeding by humans to perfect, say, sheeps’ wool.
After modifying genes that give a desired quality to a natural fiber, scientists insert this DNA into yeast or bacteria cells. Next, fermentation turns the microbes into factories, churning out proteins that will be spun into fibers and given names such as Microsilk and Werewool.
As the companies see it, the process is more efficient than growing fibers naturally; traditional silk, for example, is biodegradable and long-lasting, but cultivation can use large amounts of water and pesticides. One of the most promising polyester and silk replacements is Tandem Repeat’s squid protein-based Squitex, which draws on AI to design a fiber with stretch, strength and thermal responsiveness, and it works with most current manufacturing equipment. The Philadelphia company, which plans to sell both fibers and garments, will release a limited collection this year.
Another is Spiber’s Brewed Protein, which can replace oil-based, silk and other animal fibers. The polymer can yield various end products depending on the twisting of yarns. By changing the protein content and yarn diameter, the company can tweak texture, weight and handfeel.
Spiber Inc’s Brewed Protein filament yarns have a silk-like sheen and texture. (Photo courtesy of Spiber Inc.)
That’s the easy part, experts say. The difficulty, and the stage most of these startups are now, is in scaling manufacturing. The manufacture of next-gen fibers requires giant fermentation vats and skilled workers. When it comes to spinning, according to Bloom Labs, costs can be two to three times higher than with oil-based yarns because the melt-spun machines used by the apparel industry don’t work with these fledgling fibers.
But as the planet burns and plastic fibers boom, it’s getting harder for brands to ignore the need for sustainable fabrics.
Nicole Rawling, CEO and co-founder of the think tank Material Innovation Initiative (MII), says they define “next-gen” as more than the gene-edited proteins. Those fibers can be plant-derived, mycelium, cultivated animal cells, microbe-derived, recycled materials and blends. “Next-gen materials must be animal-free, high-performance and have a smaller environmental footprint than their traditional counterparts,” she says. MII focuses on the goals of production, not the technologies used.
“We recommend focusing on the real problem: petrochemicals, not plastics,” says Rawling, noting that some plastics are bio-based and have less of an environmental impact. The claim is controversial, however, in terms of biodegradability and because plant-based plastics require crops such as corn and farmland that could have been used to grow food.
Spiber’s Brewed Protein materials are produced through a fermentation process that utilizes sugars and microbes. (Photo courtesy of Spiber Inc.)
Proteins aside, Circ, a recycling innovator, has developed a hydrothermal process that can separate polyester-cotton blends—the largest blend category globally—and recover both portions to make into like-new fibers for textiles.
“Not long ago, it was nearly impossible to separate and re-use fibers from cotton/poly blends, thus millions of tons of discarded clothing and textiles were destined for landfill or incineration,” says Rawling.
One challenge is designing biodegradability into goods that won’t easily fall apart in use. A recent study from UC San Diego’s Scripps Institution of Oceanography tracked the ability of natural, synthetic and blended fabrics to decompose in the ocean. It found that natural and wood-based cellulose fabrics (Lyocell, Modal and Viscose) degraded within a month, while fabrics made of what was thought to be a biodegradable plastic (PLA) and the oil-based fibers in textile blends showed no decay after more than a year in the ocean.
Kintra Fibers has developed a bio-based polyester (56 percent corn-derived) it says greatly reduces greenhouse gas emissions compared to conventional polyester and can be produced with the same equipment. According to its website, the material decays in controlled composting conditions.
Fiber growers
Last October, Sally Fox was thousands of miles from home, where the greens and golds of her cotton fields shimmered in the Central Valley sun. She was at a cotton-spinning mill in Japan to sell her fibers, because there are no such mills left in California, she said in an email. “I have one customer in the world.”
Fox has been selectively breeding cotton to produce her exquisitely colored yarns for 38 years, and she says the industry was once profitable enough that she could afford to lease her own gins, the machines that quickly separate cotton fibers from seeds.
That’s no longer the case. “The textile industry collapsed when the big brands went offshore and dumped the spinners and weavers in the US, Europe and Japan. And I lost all the mills I was selling to except this one,” she said.
Fiber farmers, already up against cheap polyester and the economy of fast fashion, now face another threat: the rise of mass-produced alternative synthetics in development.
Naturally colored cotton, bred by Sally Fox, growing at her Viriditas farm in California’s Capay Valley. (Photo courtesy of Sally Fox)
Rebecca Burgess, founder of Fibershed, a nonprofit that supports regenerative farming, points out that there is already a bounty of natural fiber available for textiles.
Two-thirds of the wool in California doesn’t even have a home and 900,000 pounds per year is textile grade, says Burgess. “We’re not even getting all the natural fibers that are part of food rotations.”
The US is the third-largest global cotton producer. In 2018, more than 14 million of the 18 million bales it produced were exported. More than 200,000 acres of cotton is grown in the San Joaquin Valley—”enough to create at least seven pairs of jeans each year for every person in the state,” says Burgess.
If a strong local fiber economy existed, growers could find markets for all their fiber, she says. Instead, they face “huge deficits” in aggregation, distribution and manufacturing. If you start a spinning mill, for example, you also need a good wool scour line for a washing station and places to send wastewater.
Absent is large-scale felting, wool scouring, color-grown cotton gins, large-scale fine gauge spinning, industrial felt natural dye pigment production and more.
Burgess sees the main problem with cheap fashion—one she thinks next-gen won’t solve—as massive overconsumption. At one end are people unboxing their huge hauls, “stoking people on TikTok to purchase just like them.” At the other is the Atacama Desert in Chile or Accra in Ghana, “where they receive something like 40 million garments per month,” most of which end up in open-air dumps.
Soil-to-soil fiber economies
Fibershed advocates for bringing home the once-thriving textile supply chain, which now exists as a geographically long series of links among growers and processors of fibers, weavers, knitters, dyers and finishers, product manufacturers and distributors. It envisions local systems where natural fibers are sustainably grown, processed, sewn into garments and ultimately composted.
In Fibershed’s 168-producer network are regenerative farms and textile projects such as Chico Flax in the Sacramento Valley, which is working on bringing back the region’s flax textile industry. There are growers of dye plants, hemp, cotton and wool.
Wool production is often criticized for wreaking havoc on land, from overgrazing to scouring chemicals. The Center for Biological Diversity has called on brands to phase out or cut wool use in half by 2025. But Fibershed sees wool as a carbon sink. More than 55 wool producers have joined its Climate Beneficial™ Verification label program that supports farmers who are building healthy soil.
Wool is a renewable, biodegradable resource, but critics say the current scale of wool farming is environmentally unsustainable. (Photo: Shutterstock)
It’s not about small versus large-scale farming, says Burgess; small growers don’t always have enough land to use the rotational grazing that fosters plant biodiversity. “Some of the most regenerative, or grassland regenerating, grazing I’ve seen is on larger operations.”
To create vegetation shifts and poly cultures, ranchers try to mimic a wildland biome through multi-species grazing, “moving animals quickly through these systems, then having them return after land has had time to regenerate.”
Even cotton can be grown and processed within a scalable, restorative system, proponents say. Central Valley growers and researchers are incorporating carbon farming to help soil store carbon and water; abilities lost to decades of conventional practices. Less than one percent of cotton grown in the US is organic.
Cotton growing at Viriditas Farm, where rotational crops like heirloom Sonora wheat bolster root material and straw to build soil organic matter with each crop year. (Photo courtesy of Sally Fox)
Cleaning up cotton is something Sally Fox knows all about. “I was among those who started the whole organic cotton industry.” She grows her colorful “foxfibre” cotton using biodynamic practices, but for certification, she sticks with organic—it’s less challenging, but organic is the original regenerative certification, she says.
“It is absolutely the gold standard for sequestering carbon into soils—the goal of all regenerative farming practices.”
Unbox ‘like new’
Fox views sustainability in clothing as revolving around its longevity. Cotton spun correctly should last 20 to 60 years (except jeans). Linen spun correctly should last 100 to 1,000 years. Wool spun properly should last 80 to 300 years. “I am not kidding,” she emphasizes.
Her next criteria is ethical production, “with the work force between the raw material and final product not being enslaved or coerced or any of the rest of the shenanigans used to beat down the cost brands pay for products.” She prefers garments made in the US, Japan or the EU, because they have workplace standards. Elsewhere, she seeks GOTS and Oeko-Tex certifications. “GOTS actually inspects every facility.”
Last but not least, she mends holes, fixes seams. She even darns socks. It’s not exactly fast fashion, but just landing on a definition of sustainable “can make one’s head spin,” she says. And the first response is to give up, and basically give in to polyester—the wonder fabric that, today, isn’t so wrinkle-free after all.
With legislation that requires end-of-life solutions for products, consumers rethinking their choices and investment in both next-gen synthetics and local natural fiber economies, both visions can be part of a better clothing future. Here’s how you can help:
Buy less, and love what you do buy. Instead of buying loads of cheap clothing, instead think about investing in a few high-quality items that you love and know will last you a long time. Whether made of synthetic fibers or natural fibers such as wool, silk and linen, keep in mind the lifecycle of your clothing: what will happen to it when you’re finished with it?
Buy and sell used clothing. Gently worn or returned purchases are increasingly being offered on sites such as ThredUp, Poshmark, Relay Goods and Patagonia’s Worn Wear. (For example, Relay, which calls itself a zero waste marketplace, sells shoes and sports gear, buying their surplus inventory and returns from retailers and offering the most sought-after shoes at attractive markdowns).
Learn to mend and repair. Sewing, darning and other forms of mending used to be common, and for good reason: they help you get the most out of your clothing, and they can be fun and creative, too. Inspiration is everywhere, if you know where to look—social media can be a good place to start, and books such as Visible Mending by Arounna Khounnoraj provide step-by-step instructions for how newbies can get started.
Support legislation designed to cut down on textile waste. Legislation introduced in California and New York would eventually require textile producers to provide end-of-life solutions for products. If you want to support those bills or ask for a similar one to be introduced in your state, contact your local legislators and let your voice be heard.